搞懂板金加工流程: 從板金設計到板金生產,走入板金加工的大小事
天源雷射帶你深度了解板金加工的流程,從板金設計到雷射、折彎與焊接等製程的解析,幫助你需要板金加工時不再被搞混,能順利的完成您的產品。
搞懂板金加工流程: 從板金設計到板金生產,走入板金加工的大小事
前言
板金加工廣泛應用於各類型產業,如:機械外罩、廚房不鏽鋼設備、半導體設備等,此外,在你我生活周遭亦可以隨處看見鈑金產品的身影,如:電腦機殼、微波烤盤、通風過濾設備甚至是手機架等等,都是板金加工的成果。現在讓我們共同來進入板金加工的流程,從板金3D設計、雷射切割到焊接組裝等,了解這歷久彌新的產業。此篇文章主要針對以黑鐵板、白鐵板為基材進行二次加工的板金加工(Sheet Metal Fabrication)行業,汽車外鈑金屬於金屬成型領域,將不在此範疇討論。
.png)
板金加工回顧
"板金加工"與“鈑金加工"兩個詞都廣泛應用,"板金加工"代表於平面塊狀物上進行加工,而“鈑金加工"明確指出其於金屬物體上進行加工,如黑鐵、不鏽鋼及鍍膜材質鍍鋅板等,在本文採用板金加工做為主要,鈑金將用於製成之金屬產品。板金加工歷史(1)起源可以追朔於上個世紀,用於建造刀和武器等。於工業革命時期,慢慢發展出以剪(Shear)及成型等對於鍛造出的鋼鐵進行質變,進而衍伸出剪床及沖孔(Punching)加工等形式,透過物理接觸將板材進行切割或者成型。
目前主流的板金加工以雷射切割為主,主要可分為二氧化碳(CO2)及光纖雷射切割兩種形式,光纖雷射的節能與高單位面積功率的優勢,逐漸成為板金加工的主流。切割後的零件透過折彎刀具進行成型,由於每個材料有其延展(Deforming)性,因此折彎優劣往往決定精度之好壞。焊接與組裝將零部件進行組合,產生出客戶所預期的鈑金成品。以下將針對板金加工流程進行分站式介紹。
.png)
板金設計
板金設計是接單後最為關鍵的環節,客戶的需求與加工條件能否有效地傳達到客戶端,取決於板金設計團隊的經驗與細心,主要包含以下流程
- 3D板金設計:3D設計有時並無法直接用於板金加工,如缺少折彎曲率標示等,板金廠會協助轉換該設計為板金加工圖,並確認零件之間或者加工時期是否有干涉產生。
- 展開至2D板金工程圖: 透過計算材質延展性,或稱裕度(Deduction),將3D圖展開為2D板金圖。亦有廠商直接以2D繪製板金加工圖,但在干涉的確認上會變得較為困難。
- 標註尺寸及加工要求: 針對鎖附孔、特殊切割縫隙標註尺寸,並於工程圖面上備註客戶需求(如板金加工急件、表面要求等)。近年來也逐漸有板金加工廠以無紙化方式傳遞工程圖面,以確保不會因為髒污或遺失延誤交期。
- 轉換成雷射切割之圖檔: 由於工程圖包含尺寸及標註,並無法直接用於雷射切割。因此需要轉換圖檔為雷射圖,其中包含切割圖層與雷射雕刻圖層(Engraving),軟體即可自動識別加工模式。
.png)
板金排版及程式製作
板金加工的排版環節往往容易被忽略,其主要包含板金排版(Nesting)與轉換為機器程式(NC generation)兩個步驟,能否切割出合宜的板金工件在此階段已經決定
- 板金排版: 由於常見之鐵板為 5尺x10尺(3050mm x 1525mm) 及 4尺x8尺 (2440mm x 1220mm),需要將多個相同材質與厚度的材質進行組合併入同一塊板材。對於有砂面要求客戶,優秀的板金加工廠商會調整工件方向,達到良好的金屬紋路呈現。
- 程式製作: 排版後的結果,需要轉換為機器可以讀取之板金加工程式,加工斷面的處理、R角甚至是精度將於程式製作決定。由於科技的進步,現場師傅程式輸入除了速度緩慢外也容易產生問題,建議選擇有優秀排版團隊之板金加工廠。
.png)
雷射切割
雷射切割主要分為CO2雷射切割與光纖雷射切割兩種,以下針對兩種雷射切割優劣勢進行分析,協助您選擇良好的板金加工合作夥伴
- CO2雷射切割: CO2雷射切割被廣泛用於金屬與非金屬的切割,然而由於其高耗能及高維護成本的特性,於板金加工行業逐漸式微。然而值得一提的,由於其針對不鏽鋼斷面加工的優勢,有規模的板金加工廠依然會採用,來因應客戶不同的需求。
- 光纖雷射切割: 光纖雷射近年來成為板金加工廠的新寵,其高速加工及節能特性符合永續經營的要求。不過值得注意的,光纖雷射的高速切割及人力短缺的狀況,板金加工廠有無能力整合雷射於自動化倉儲設備將是品質與交期的關鍵。
.png)
折彎成型
折彎成型工站為板金加工的咽喉,往往決定著精度與生產瓶頸,折彎成型流程與關注點如下
- 折彎程式製作: 多數折彎雖然是半手動程序,但仍然需要移動上刀模(Upper tooling)、下刀模(Lower tooling)及背規(Backgauge)至加工位置,因此需要進行程式的輸入,往往也是生產延誤或折彎尺寸錯誤的關鍵。近年來,開始有板金加工廠透過折彎軟體快速產生程式,改善生產的瓶頸。
- 折彎成型機(或稱折床): 折床一般以油壓方式驅動,有其最大可以產生的壓合力,進一步也決定了其最大可以加工的厚度。此外,由義大利率先提出的多邊折彎中心機,透過下刀模的高速成型,可以產生近似圓弧的折彎角,是技術的一大突破。
除此之外,折彎上接雷射下接焊接,為調整板金生產節奏的環節,因此其搬運(半成品台車)及自動化技術(自動換刀系統)等,都是決定該板金加工廠能否準時遞交鈑金件至客戶的關鍵。
.png)
焊接與組裝
焊接與組裝工站將成型之工件組合,由於此工站為板金成品的末端並決定組件的強度,建議與專業的板金加工廠討論來決定適合的組立方式,常見的方法如下:
- 機械式組裝: 主要以螺絲螺帽的方式進行組裝,此組裝較為彈性,後續可以自行拆裝等,多用於機殼,如電腦殼等。
- 板金焊接: 透過惰性氣體如二氧化碳和氬氣做為保護氣體,以高溫熔解進行工件的接合,不同的材料如白鐵、黑鐵等,此工藝往往可以提供長久且高強度的成品。
- 板金點焊: 點焊亦屬於焊接的範疇,主要透過點的方式接合兩個工件,可以較為快速的進行焊接,然而其強度無法無上述的板金焊接。
- 鉚釘式組裝: 相較於焊接,鉚釘可以提供低成本且高強度之特性,此經濟實惠的組裝方式也日益普及於板金加工業。
焊接與組裝工藝於不同產品差異極大,與板金加工廠的溝通往往是決定成敗的主因。尋找能以客戶為中心的板金加工供應商可以大幅減少錯誤的產生。
.png)
結語
除了上述提及的板金設計、板金排板、雷射切割、折彎成型與焊接組裝外,其他如攻牙、整平、量測及噴漆等都是廣域的板金加工業涵蓋範圍,因此如何選擇一合作夥伴能良好的涵蓋各工藝讓您專注前端業務與設計,是一未來趨勢。此外,許多板金加工廠協助電子模組的組裝,此類的機電整合需要廠商擁有板金加工與電腦檢測的業務經驗,又或者是板金加工結合外型設計等,此跨領域的整合亦逐漸成為不可忽視的趨勢。
板金加工是一高耗能的產業,在強調永續經營與低碳排的未來,板金加工的碳排放將被高度的關注,因此建議在尋求板金加工廠商除了硬體的專業外,永續經營的理念,甚至是數位轉型的執行也是需要了解的重點,如此才能有長期且穩定的合作,確保板金加工供應商可以提供最完善與即時的硬體與軟體服務。
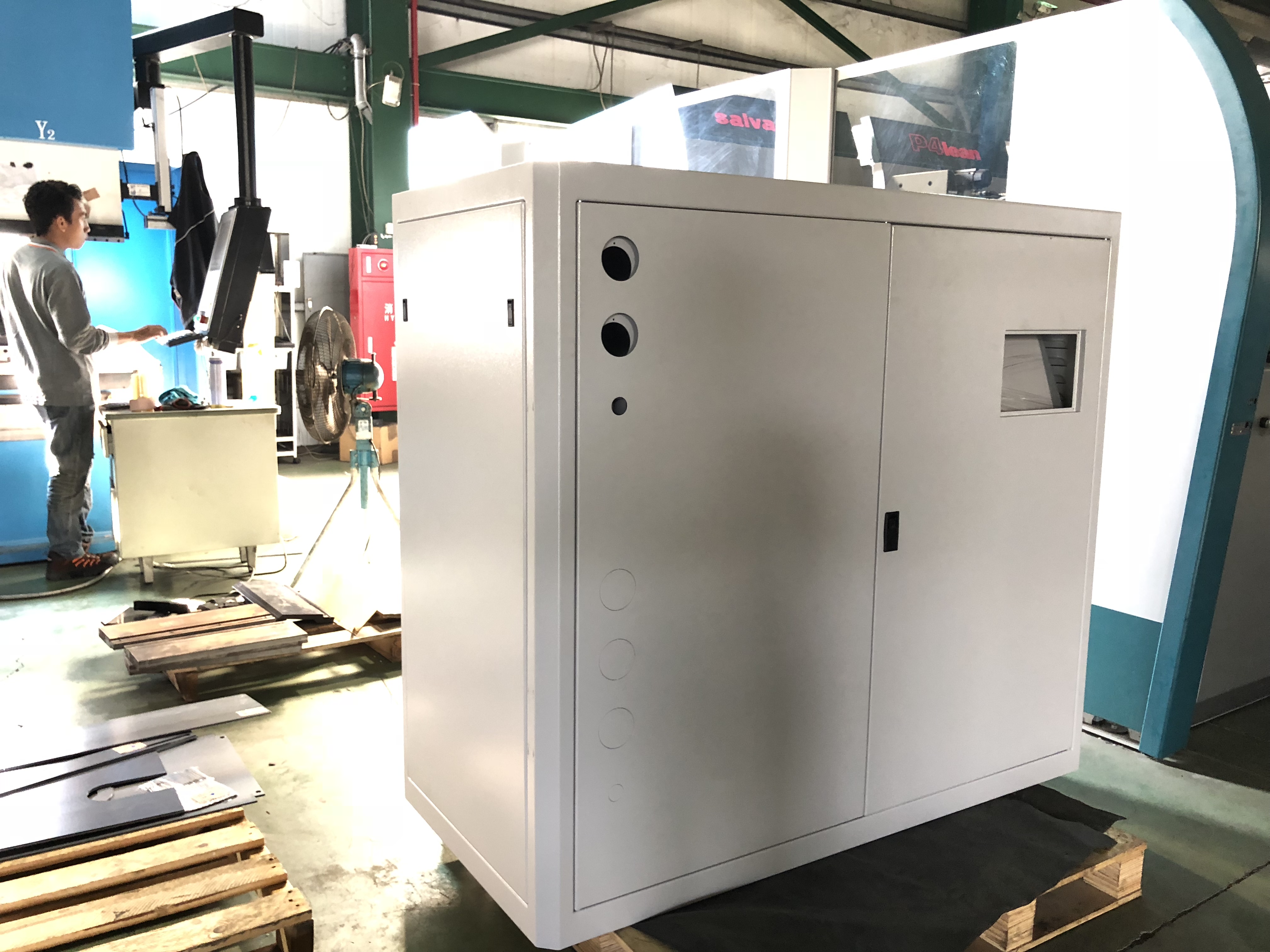
天源雷射板金加工一站式生產
聯絡地址: 台中市烏日區溪南路一段506巷418弄125號
聯絡信箱: service@airforce.com.tw
聯絡電話: 04 2335 5036